Natural Graphite Processing Equipment
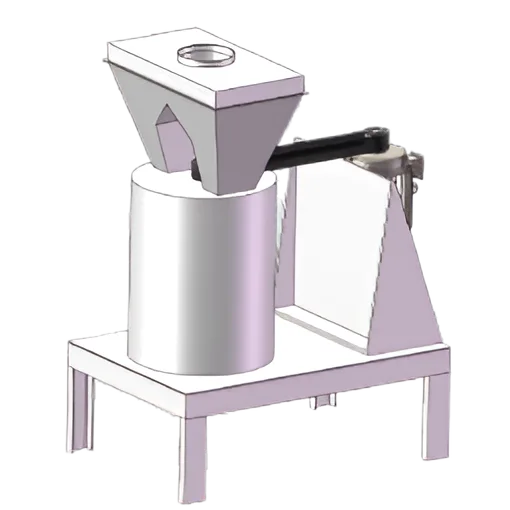
Crushing Equipment – Composite Crusher
The composite crusher applies to the crushing process of natural graphite.Natural graphite falls vertically from the upper part ofthe machine into ahigh-speed rotating impeller, under the action ofhigh-speed centrifugalforce,it colides and crushes at hizh speed with another pat ofthe materiathat is distributed in a state around the impeller. After the materials collide with each other,they willform vortices between the impeller and theiasing and colide and rub against each other multiple times to crush them., They are discharged directly from the lower part, forming a closed loopwith multiple cycles, and controlled by screening equipment to achieve the particle size of product.
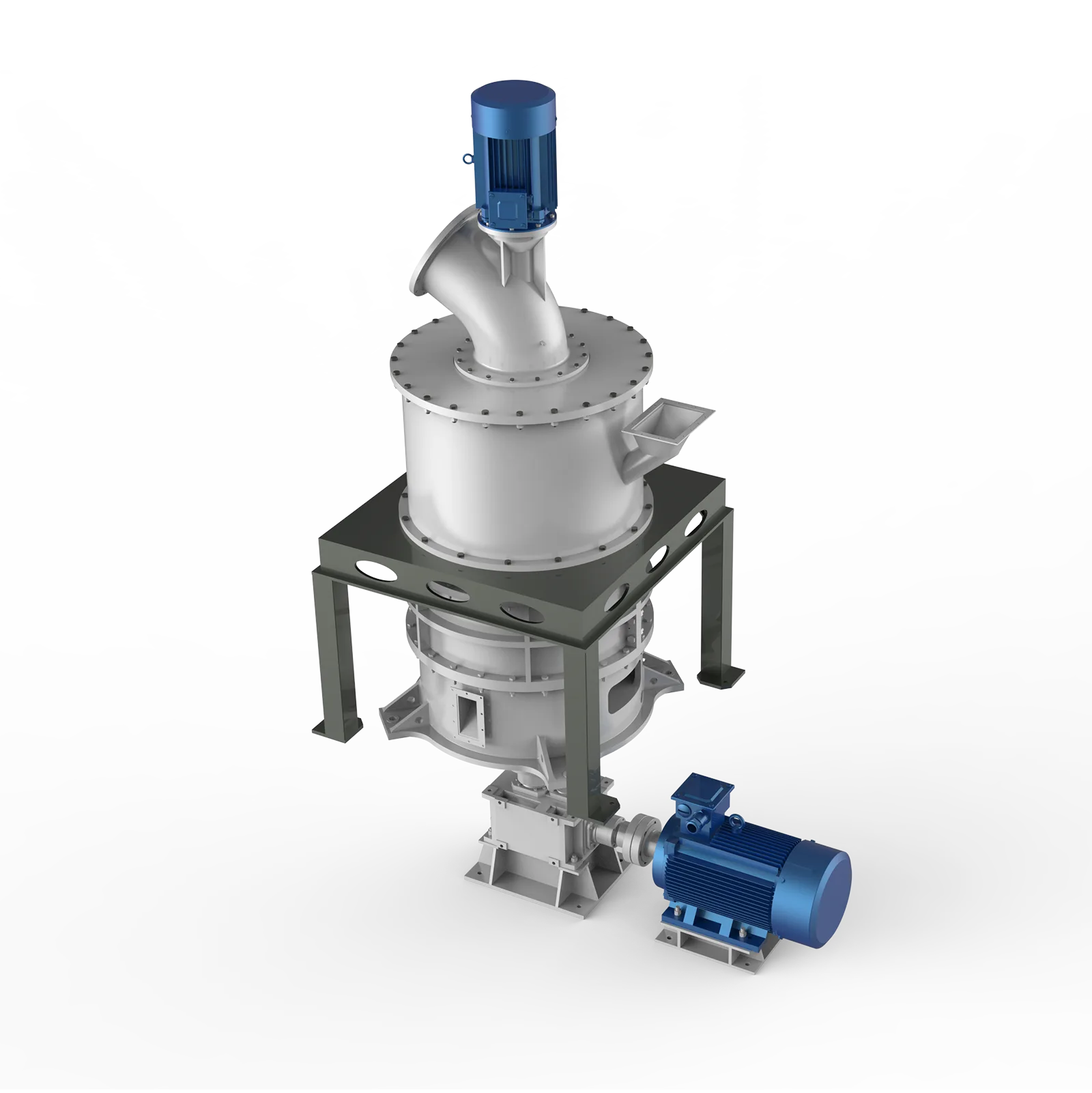
Grinding Equipment – Ring Roller Mill
ZDZN TECH has independently developed high-performance ring roller mills and shaping machines, designed for the mechanical spheroidization of natural graphite.
The ring roller mill efficiently grinds flake graphite into fine powder, creating favorable conditions for the subsequent shaping process. During grinding, the powder surface is modified, enhancing specific surface area and tap density. These improvements significantly boost electrochemical performance, leading to higher first coulombic efficiency, greater reversible capacity, and excellent cycle stability in lithium-ion batteries.
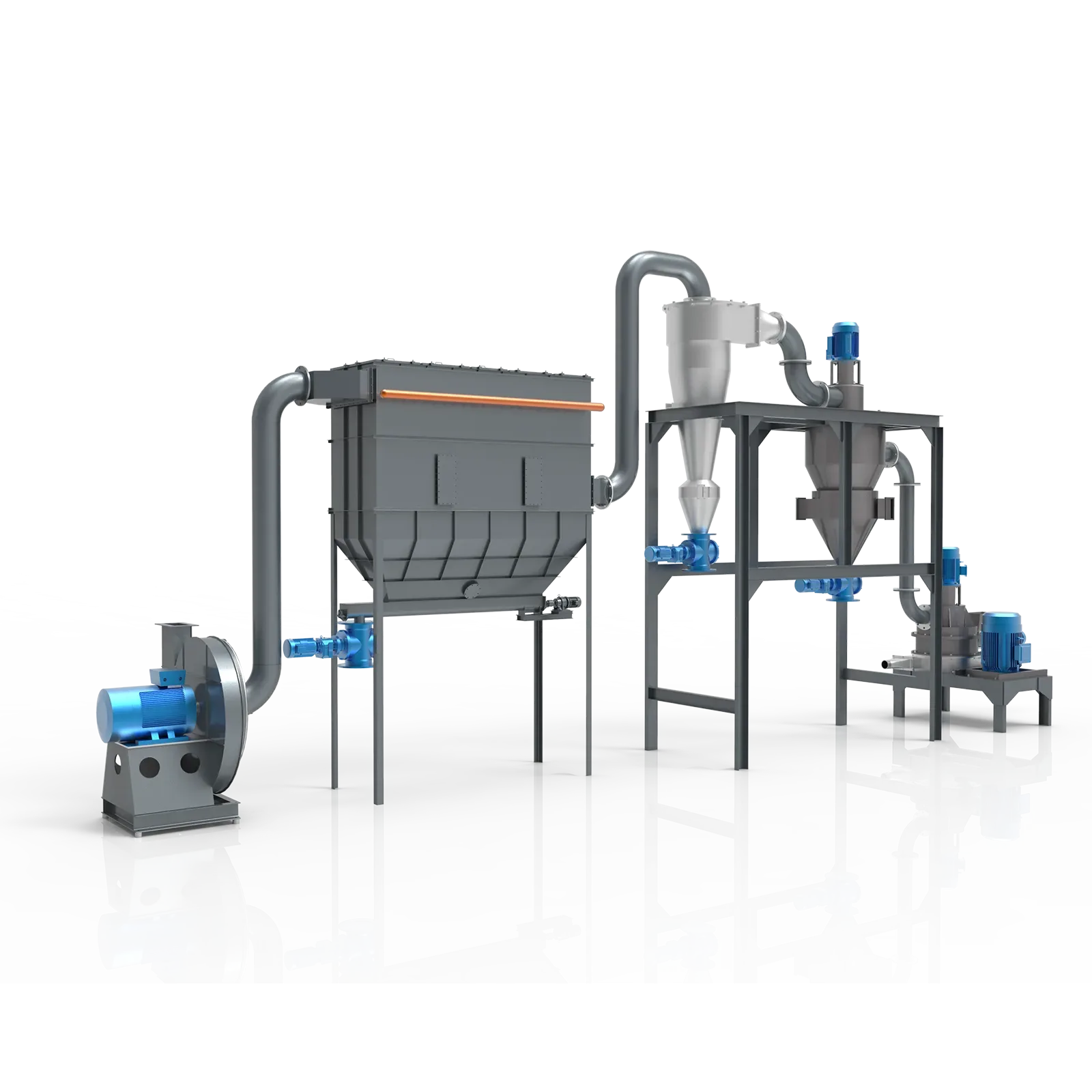
Grinding Equipment – Spheroidizing Machine
ZDZN TECH has independently developed spheroidizing machines and ring roller mills, specifically designed for the mechanical spheroidization of natural graphite.
In this process, flake graphite is transformed into spherical particles while the powder surface is simultaneously modified. This significantly enhances the electrochemical performance—improving specific surface area and tap density—which leads to higher initial coulombic efficiency, greater reversible charge/discharge capacity, and excellent long-term cycle stability.
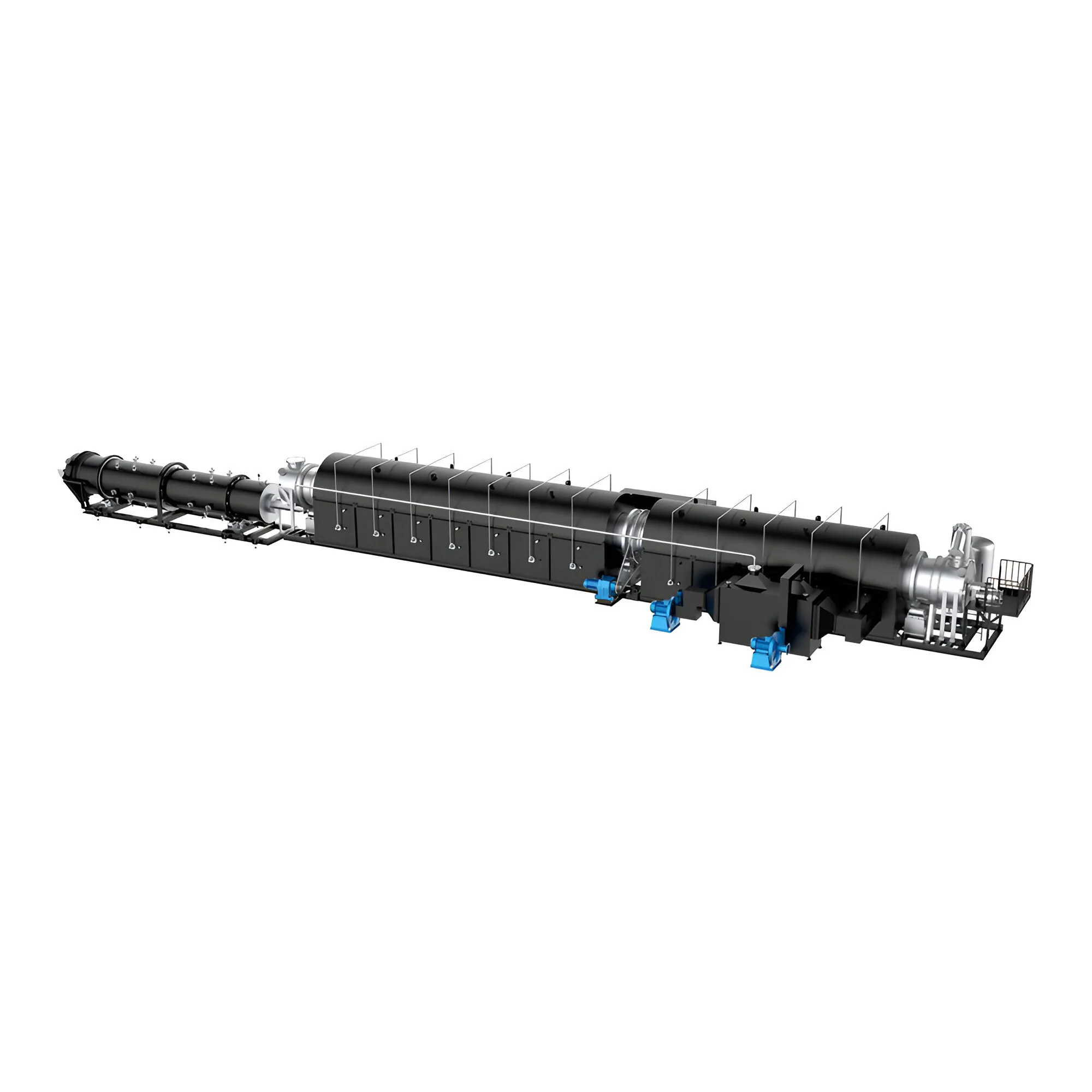
Rotary Furnace-Internal Combustion
The internal combustion coated granulation rotary furnace is used for the surface modification of natural graphite. It adopts natural gas heating and preheating recovery technology to reduce energy consumption and operational costs. During the heating process, a layer of amorphous carbon is coated onto the surface of natural graphite, effectively filling defects in the graphite layers. This enhances the electrochemical performance of graphite electrode materials and makes the equipment well-suited for continuous, large-scale production.
Equipment Dimensions: 56×4.2×5.5m
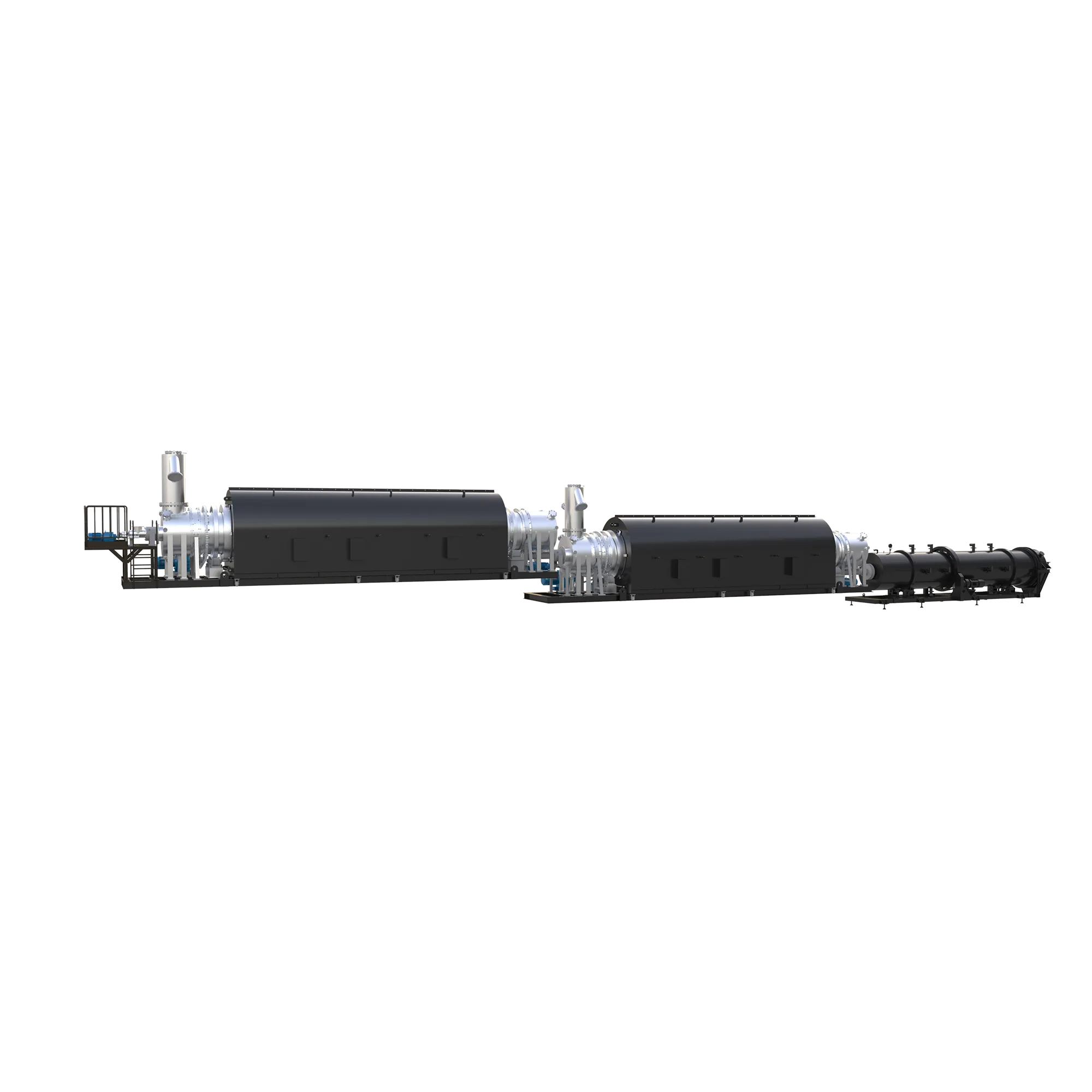
Coating Granulation – Rotary Furnace
ZDZN TECH has independently developed high-performance ring roller mills and shaping machines, designed for the mechanical spheroidization of natural graphite.
The ring roller mill efficiently grinds flake graphite into fine powder, creating favorable conditions for the subsequent shaping process. During grinding, the powder surface is modified, enhancing specific surface area and tap density. These improvements significantly boost electrochemical performance, leading to higher first coulombic efficiency, greater reversible capacity, and excellent cycle stability in lithium-ion batteries.
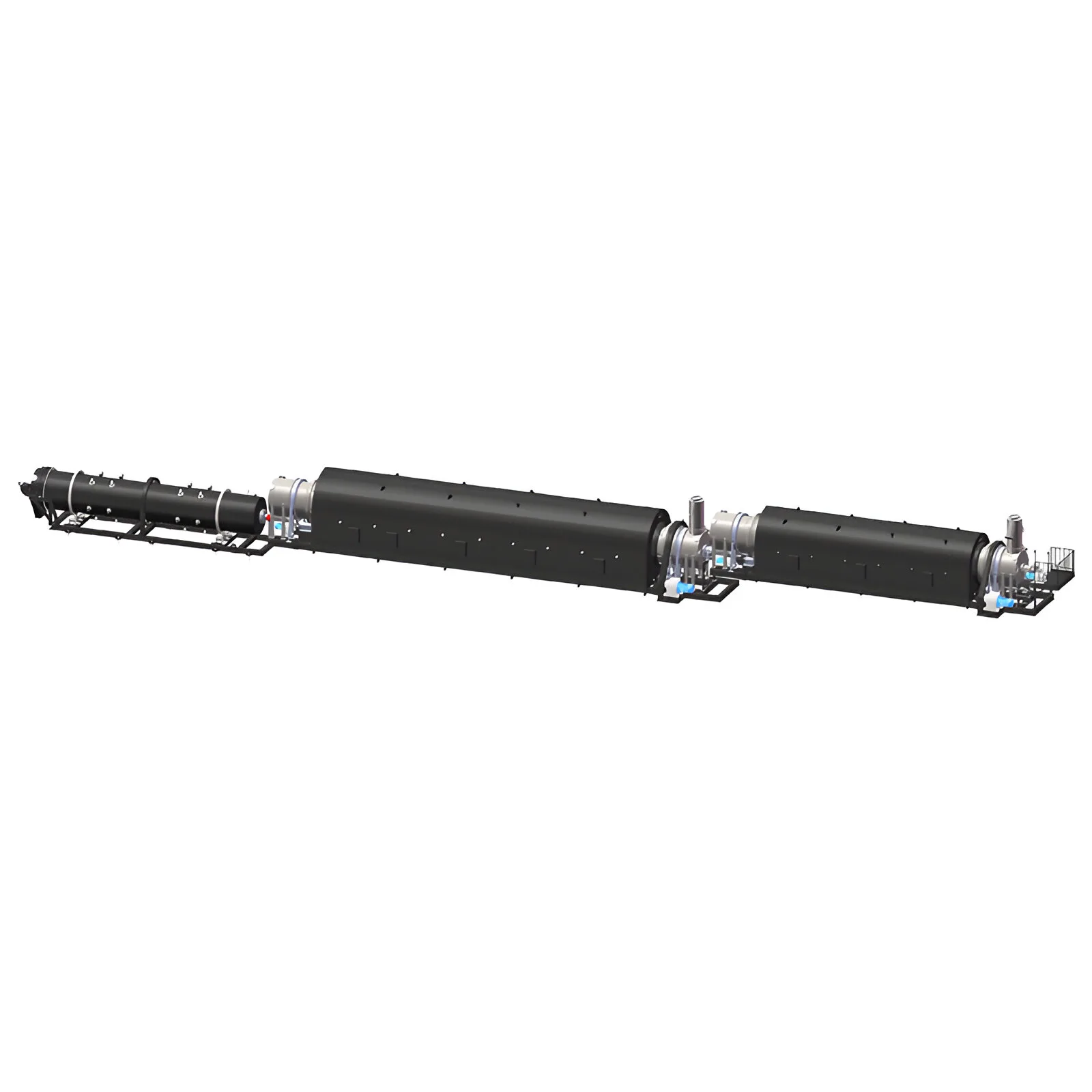
High Temperature Carbonization Rotary Furnace
The high-temperature carbonization rotary furnace is used for the high-temperature carbonization process of natural graphite. Inside the furnace, graphite is coated with a layer of asphalt or resin-based polymer material at temperatures below 1200 °C. This coating helps prevent the co-embedding of small organic molecules, thereby further improving the rate performance and cycling stability of the anode material.
Equipment Dimensions: 47.9×3.8×5.7m
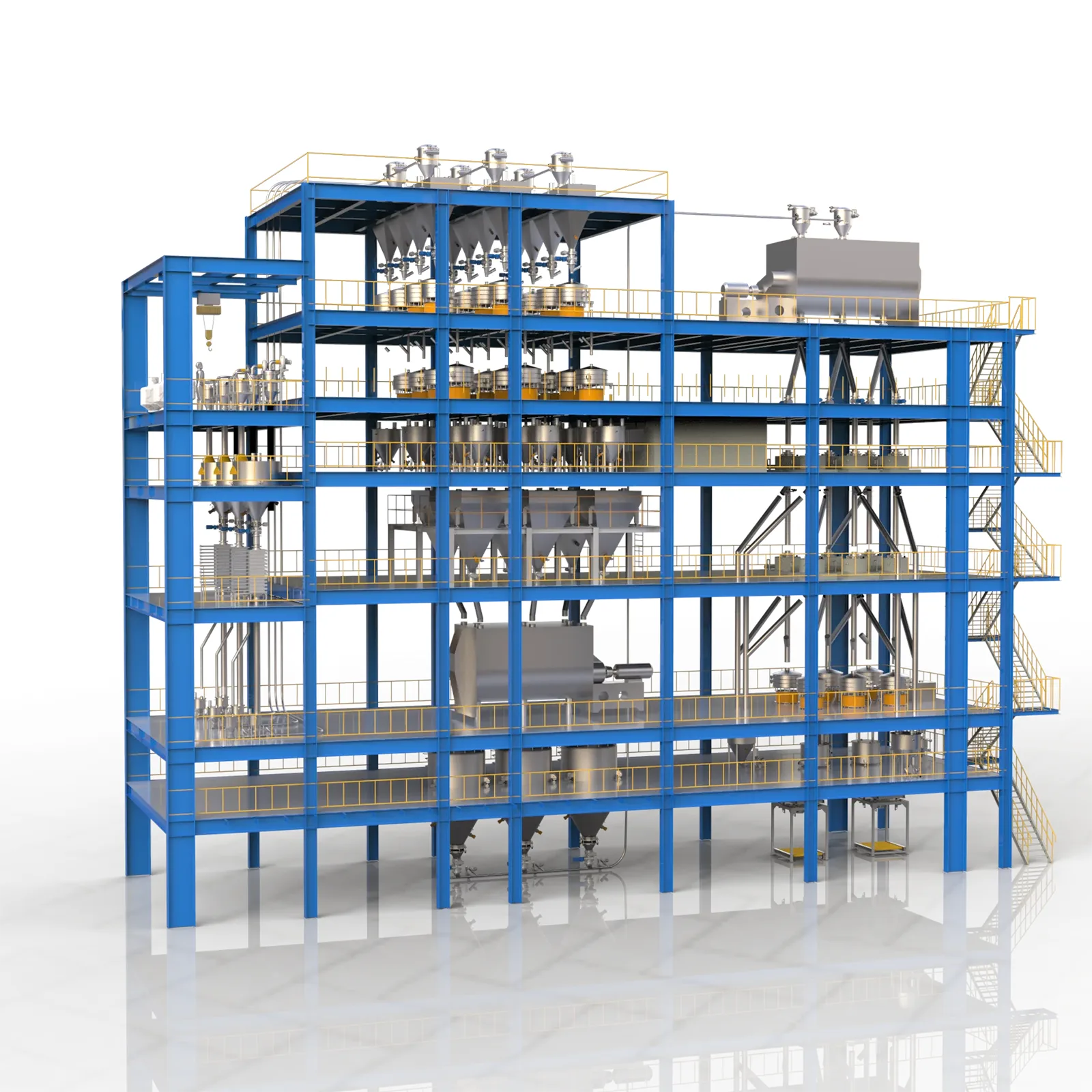
Final Product Handling System
The final product handling system is used for the screening and demagnetization of natural graphite, and includes integrated mixing, screening, demagnetization, and packaging systems. The production line adopts a negative-pressure pneumatic conveying system to minimize dust leakage and material contamination. An intelligent control system manages each stage of the production line, ensuring efficient and stable operation.
Request a Custom Equipment or Solution
Tell us your material, capacity, and process needs — we’ll tailor the right solution for your production line.